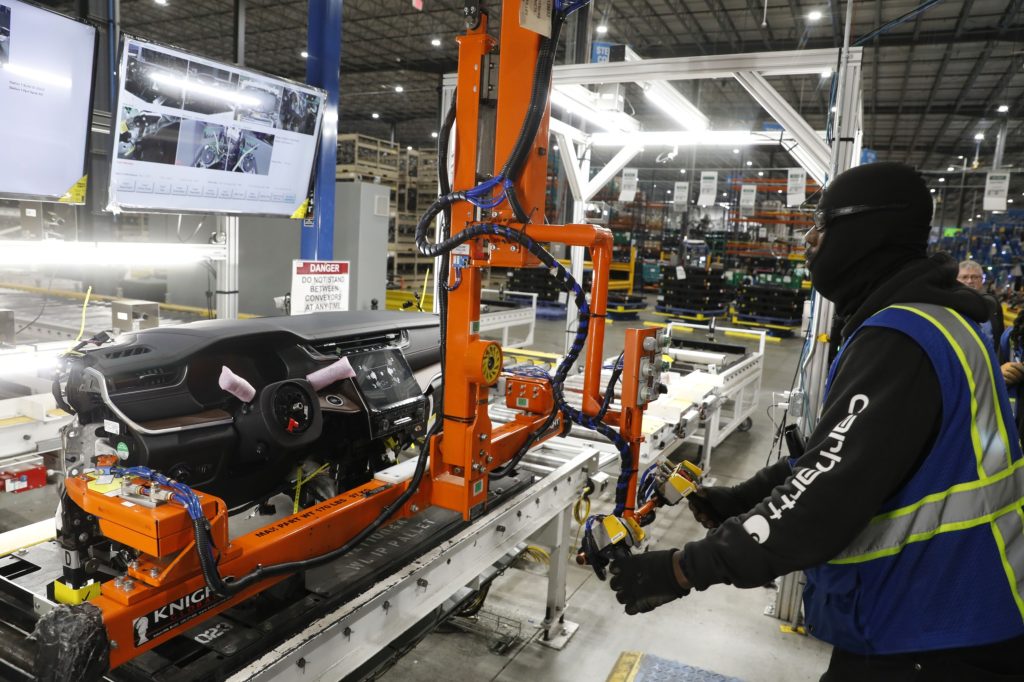
The future of manufacturing is being rewritten as companies brace for dramatic shifts in U.S. policy and global trade dynamics. As economic pressures mount and political landscapes evolve, the need for robust supply chain resilience and disruption management has never been more critical. With significant policy changes on the horizon, businesses must reassess their domestic manufacturing strategies to safeguard margins and secure a competitive edge.
Navigating Policy Shifts and Economic Pressures
Recent developments indicate that the U.S. election could profoundly alter the domestic manufacturing calculus. During the pandemic years, companies learned the hard way that investing in supply chain security and building agile manufacturing strategies is paramount. With stabilized inventory levels and easing inflation in 2024, firms are cautiously optimistic—but the incoming Trump Administration, set to take office in early 2025, is expected to implement policies that could reshape the industry. Lower corporate tax rates combined with higher tariffs on imported goods may tilt the balance in favor of onshore or nearshore manufacturing, providing a fresh impetus for reshoring initiatives. For example, studies from the National Bureau of Economic Analysis show that significant tax cuts have already spurred domestic investment, and a potential further reduction in the corporate tax rate from 21% to 15% could intensify this trend.
Tariff policies are also poised to have a profound impact. President-elect Trump’s campaign promises of blanket tariffs ranging from 10% to 25% on imports—and even higher for Chinese goods—signal a move toward protectionist measures designed to bolster domestic production. Historical precedents, such as the Australia-China trade war, illustrate that aggressive tariffs can dramatically shift market shares, forcing companies to reconfigure their supply chains. Moreover, the impending review of the United States-Mexico-Canada Agreement (USMCA) in 2026 introduces further uncertainty. Changes in the USMCA or a potential U.S. exit could affect supply chains for industries like electric vehicles, intensifying pressure on companies to prepare for both demand surges and potential retaliatory measures.
Optimizing Operations Amid Disruption
In this volatile environment, the ability to drive operational efficiency is a critical lever for survival. Companies with mature sales, operations, and inventory (S&OP) processes are better positioned to weather short-term disruptions and capitalize on emerging opportunities. As global supply chains adjust to new tariff regimes and fluctuating consumer demand, businesses must reexamine their internal processes to optimize costs and maximize productivity.
For firms expecting increased demand, it is essential to enhance cross-functional collaboration. Internally, aligning sales, production, and procurement functions can create a unified approach to ramp up production when market conditions are favorable. Conversely, those anticipating a downturn due to retaliatory tariffs must focus on cost optimization—reevaluating product portfolios, rationalizing SKUs, and potentially consolidating manufacturing footprints. Leveraging digital tools and AI-driven forecasting can help predict shifts in demand with greater accuracy, enabling a swift response that minimizes overstock and reduces holding costs.
Manufacturing transitions—whether through greenfield or brownfield initiatives—require careful evaluation of existing capabilities and assets. Decisions such as transferring equipment versus investing in new technology can significantly affect capital expenditures and operational efficiency. Additionally, managing regulatory differences and ensuring smooth knowledge transfer are critical steps when relocating manufacturing operations. Companies must also navigate rising labor costs and sourcing challenges to maintain a lean, agile supply chain that delivers timely results.
Strategic Realignment for a Resilient Future
The uncertainties of the next few years compel companies to adopt a proactive approach toward reshoring or near-shoring their manufacturing operations. Evaluating supplier reliability, securing long-term warehousing contracts, and renegotiating procurement terms are all strategies that can mitigate risks while positioning the business for growth. As the policy landscape remains fluid, businesses must build flexibility into their supply chains, ensuring that they can pivot quickly in response to new tariffs, shifting regulatory standards, and evolving market demands.
In summary, economic constraints and anticipated policy changes are set to transform domestic manufacturing. By focusing on supply chain resilience and strategic disruption management, companies can safeguard margins and unlock long-term growth opportunities. Now is the time to reengineer operations, embrace agile manufacturing strategies, and prepare for a future where domestic production becomes not only a competitive advantage but a cornerstone of sustainable success.